Czeka nas rewolucja w operacjach biodra. Pacjenci dostaną identyczny staw
2024-05-20 20:32:12(ost. akt: 2024-05-20 20:50:59)
Idealne implanty stawów biodrowych czy nowoczesne rozwiązania w zakresie chirurgii rekonstrukcyjnej można już wydrukować – i to nie jako eksponat do ćwiczeń anatomii, ale jako produkt medyczny, dzięki któremu pacjenci mogą odzyskać pełną sprawność
Badania nad personalizowanymi implantami prowadzi dr hab. inż. Patrycja Szymczyk-Ziółkowska z Wydziału Mechanicznego PWr. – To są badania praktyczne. Odpowiadają na zapotrzebowanie nas, lekarzy, ale przede wszystkim – pacjentów – mówi prof. Szymon Dragan, ortopeda z 4. Wojskowego Szpitala Klinicznego we Wrocławiu i pracownik Politechniki Wrocławskiej.
Nasz staw biodrowy przy zwykłym spacerze musi znieść obciążenie równe 4-5-krotności naszej wagi ciała. Jeszcze większe, nawet dziesięciokrotne, w przypadku biegu czy jazdy na nartach. – Pacjenci przychodzą z bólem, chcieliby nadal cieszyć się życiem, być aktywnymi. A nasze ciało nie jest maszyną – tłumaczy lekarz od lat współpracujący z Wydziałem Mechanicznym.
Dla niektórych pacjentów nadzieją jest zabieg wszczepienia endoprotezy biodra lub kolana. W naszym kraju wykonuje się ich ponad 50 tys. rocznie. Jednak 8 proc. pacjentów wraca do szpitala, a jednym z powodów może być brak dopasowania do anatomii pacjenta.
Zamienniki z tytanu
Większość obecnie stosowanych implantów ortopedycznych ma znormalizowany kształt o określonych rozmiarach. To stanowczo za mało.
– Każdy przypadek, pomimo wielu cech wspólnych dla danej populacji, posiada również wiele cech osobniczych. Aby jak najlepiej dostosować implant do pacjenta, musimy sięgnąć do medycyny spersonalizowanej. Dzięki technologiom przyrostowym jesteśmy w stanie stworzyć implant „na wymiar”, uwzględniając unikalne cechy budowy każdego chorego – tłumaczy badaczka.
Większość obecnie stosowanych implantów ortopedycznych ma znormalizowany kształt o określonych rozmiarach. To stanowczo za mało.
– Każdy przypadek, pomimo wielu cech wspólnych dla danej populacji, posiada również wiele cech osobniczych. Aby jak najlepiej dostosować implant do pacjenta, musimy sięgnąć do medycyny spersonalizowanej. Dzięki technologiom przyrostowym jesteśmy w stanie stworzyć implant „na wymiar”, uwzględniając unikalne cechy budowy każdego chorego – tłumaczy badaczka.
Cały proces zaczyna się od zobrazowania chorego z wykorzystaniem tomografii komputerowej lub rezonansu magnetycznego. Następnie inżynier w porozumieniu z chirurgiem na podstawie uzyskanych danych 3D opracowują idealny model implantu, dopasowany do ubytku w tkance kostnej, którą ma zastępować.
Stopy tytanu stanowią podstawowy materiał do produkcji implantów długoterminowych w ortopedii i stomatologii. Nowe trendy w ich rozwoju przeznaczone do zastosowań w inżynierii biomedycznej umożliwiły rozwój stopów składających się z nietoksycznych (pozbawionych m.in. aluminium i wanadu) oraz niewywołujących reakcji alergicznych pierwiastków.
Naśladowanie natury
Tak przygotowane implanty są następnie wygładzane bądź wręcz przeciwnie, celowo pozostawia się nierówności w postaci przyczepionych do ich powierzchni ziaren proszku (co wynika bezpośrednio z przyrostowego procesu wytwarzania). Implanty wykorzystane np. do rekonstrukcji stawów w tak zwanych parach ciernych powinny być idealnie gładkie, natomiast takie, które mają zastąpić ubytek i połączyć się z otaczającymi fragmentami tkanki kostnej „lubią” chropowatości – wyjaśnia dr hab. inż. Patrycja Szymczyk-Ziółkowska. – Dzięki drukowi 3D chorzy, u których w wyniku m.in. choroby nowotworowej czy wypadku powstały rozległe ubytki w obszarze twarzoczaszki, dosłownie odzyskują swoje oblicze, mogą spojrzeć w lustro – wyjaśnia badaczka.
Tak przygotowane implanty są następnie wygładzane bądź wręcz przeciwnie, celowo pozostawia się nierówności w postaci przyczepionych do ich powierzchni ziaren proszku (co wynika bezpośrednio z przyrostowego procesu wytwarzania). Implanty wykorzystane np. do rekonstrukcji stawów w tak zwanych parach ciernych powinny być idealnie gładkie, natomiast takie, które mają zastąpić ubytek i połączyć się z otaczającymi fragmentami tkanki kostnej „lubią” chropowatości – wyjaśnia dr hab. inż. Patrycja Szymczyk-Ziółkowska. – Dzięki drukowi 3D chorzy, u których w wyniku m.in. choroby nowotworowej czy wypadku powstały rozległe ubytki w obszarze twarzoczaszki, dosłownie odzyskują swoje oblicze, mogą spojrzeć w lustro – wyjaśnia badaczka.
Także Narodowy Fundusz Zdrowia zauważył potrzebę takiego rozwiązania. W danych za 2022 rok odnotowano, że sfinansował już 78 zabiegów z wykorzystaniem personalizowanych implantów. Źródło: Politechnika Wrocławska
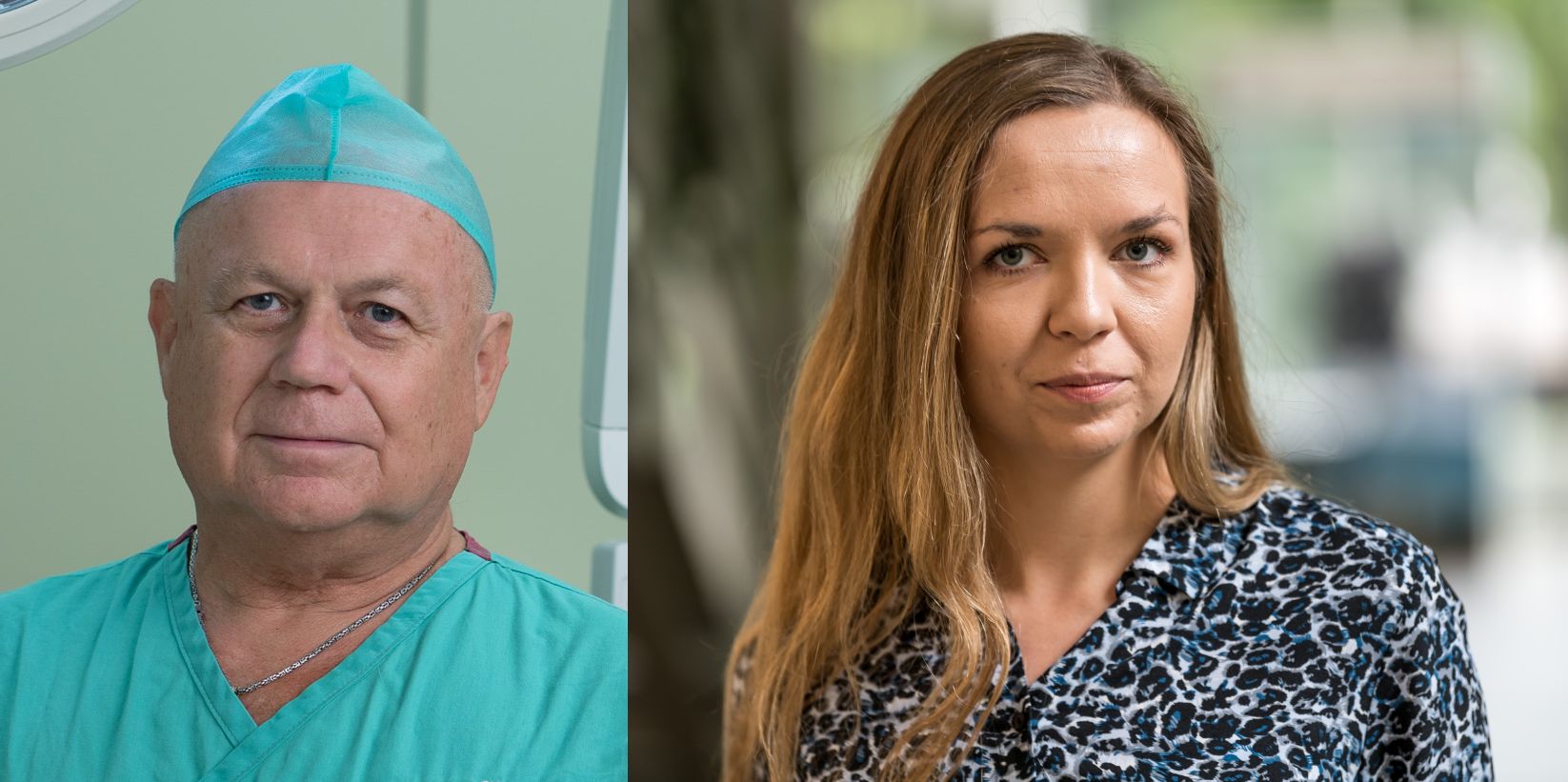
Komentarze (0) pokaż wszystkie komentarze w serwisie
Komentarze dostępne tylko dla zalogowanych użytkowników. Zaloguj się.
Zaloguj się lub wejdź przez